Industrielle Automation 4.0: Die Fabrik der Zukunft
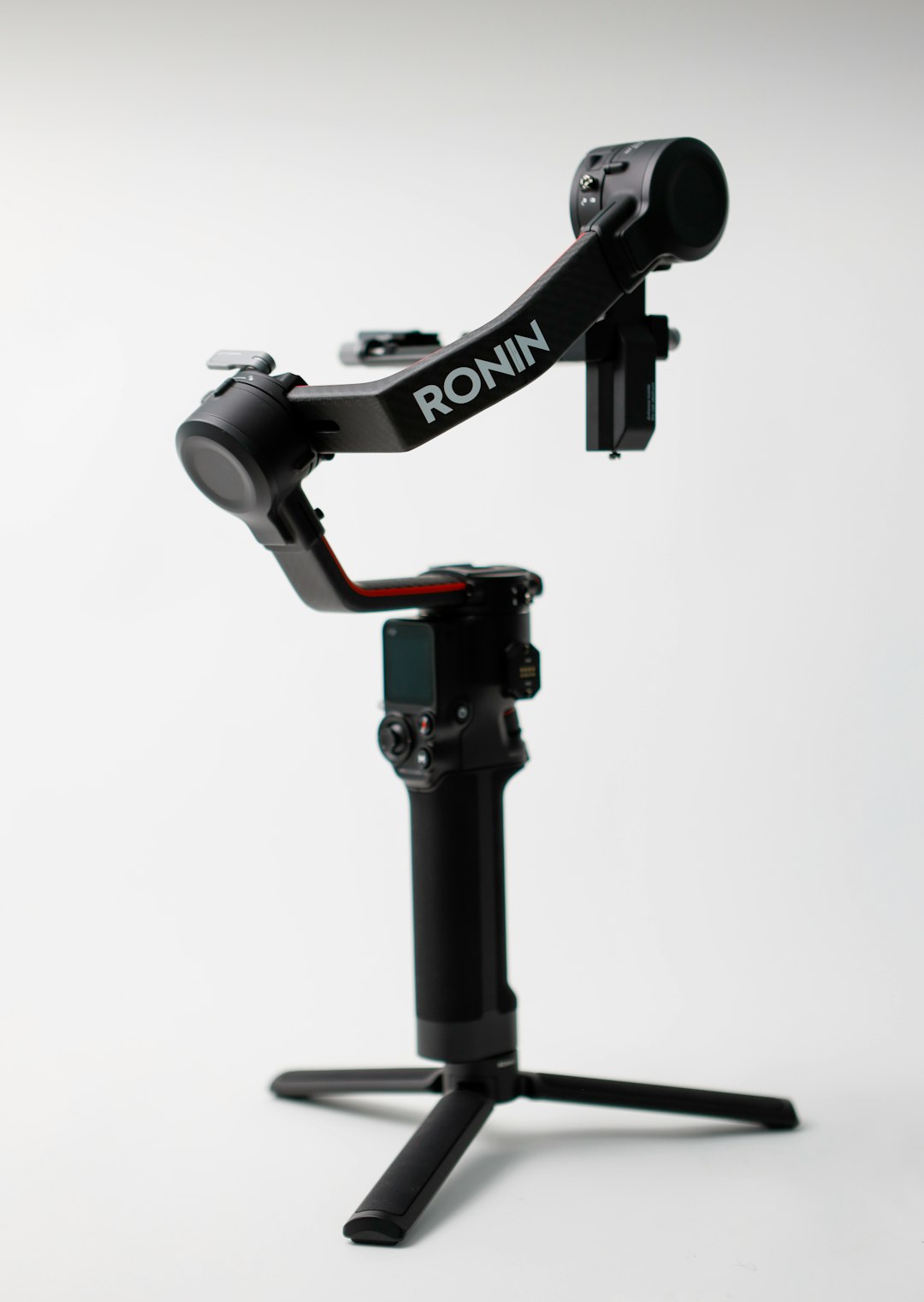
Die vierte industrielle Revolution – oder Industrie 4.0 – ist in vollem Gange. Im Zentrum dieser Transformation stehen intelligente Robotersysteme, die durch Vernetzung, Datenanalyse und künstliche Intelligenz völlig neue Fertigungskonzepte ermöglichen. Dieser Artikel beleuchtet die wichtigsten Entwicklungen und Trends in der industriellen Automation.
Von der mechanischen Produktion zur Smart Factory
Die Entwicklung der industriellen Fertigung lässt sich in vier Phasen unterteilen:
- Industrie 1.0: Mechanisierung durch Wasser- und Dampfkraft (spätes 18. Jahrhundert)
- Industrie 2.0: Massenproduktion durch Fließbänder und elektrische Energie (frühe 20. Jahrhundert)
- Industrie 3.0: Automatisierung durch Elektronik und IT-Systeme (1970er Jahre)
- Industrie 4.0: Intelligente, vernetzte Produktionssysteme (Gegenwart)
Der entscheidende Unterschied zwischen Industrie 3.0 und 4.0 liegt in der Intelligenz und Vernetzung der Systeme. Während traditionelle Automatisierung auf vorprogrammierten Abläufen basiert, können moderne Systeme selbstständig lernen, sich anpassen und mit anderen Systemen kommunizieren.
Schlüsselkomponenten der industriellen Robotik 4.0
Collaborative Robots (Cobots)
Kollaborative Roboter – oder kurz Cobots – stellen einen Paradigmenwechsel in der industriellen Robotik dar. Anders als ihre Vorgänger arbeiten sie nicht in abgeschirmten Bereichen, sondern direkt neben menschlichen Mitarbeitern. Dies wird durch fortschrittliche Sensorik und Sicherheitsmechanismen ermöglicht.
Vorteile von Cobots:
- Einfache Programmierung, oft durch Vormachen der gewünschten Bewegungen
- Flexibler Einsatz in verschiedenen Bereichen
- Geringe Einstiegsinvestitionen im Vergleich zu herkömmlichen Industrierobotern
- Optimale Nutzung menschlicher und robotischer Stärken
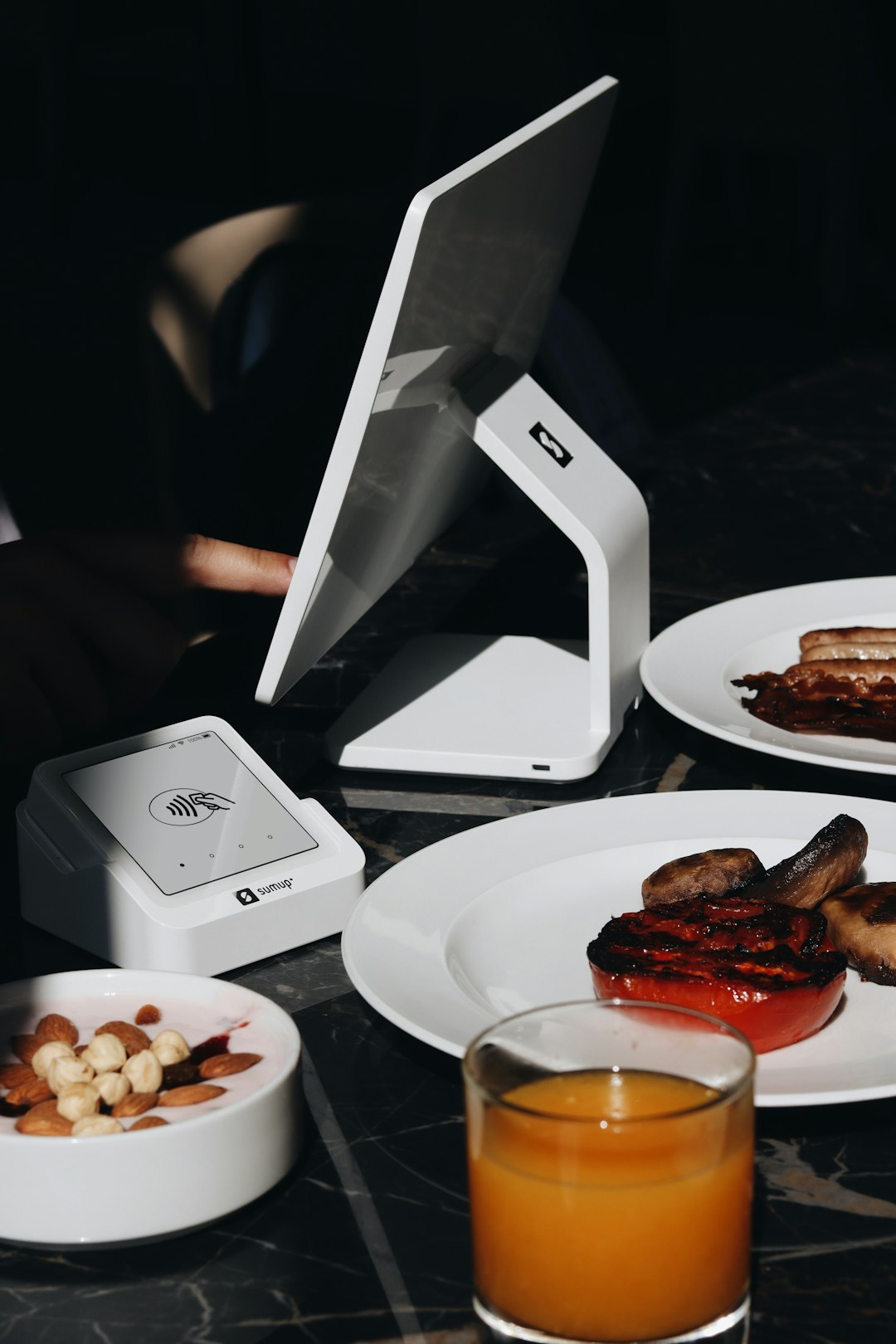
Ein kollaborativer Roboter arbeitet direkt mit einem menschlichen Kollegen zusammen
Autonome Mobile Roboter (AMR)
Die Logistik innerhalb der Fabriken wird zunehmend von autonomen mobilen Robotern übernommen. Diese Systeme können sich selbstständig in der Fabrikumgebung orientieren, Hindernissen ausweichen und optimal ihre Route planen.
Im Gegensatz zu älteren automatisierten Transportsystemen benötigen AMRs keine festgelegten Pfade wie Bodenleitsysteme. Stattdessen nutzen sie Sensoren, Kameras und KI-Algorithmen, um ihre Umgebung zu erfassen und zu navigieren.
Digital Twins und Simulation
Ein digitaler Zwilling ist ein virtuelles Abbild eines physischen Objekts oder Prozesses. In der Fertigungsindustrie werden digitale Zwillinge genutzt, um Produktionsprozesse zu simulieren, zu optimieren und zu überwachen.
Dies ermöglicht:
- Virtuelle Inbetriebnahme neuer Produktionslinien
- Predictive Maintenance (vorausschauende Wartung)
- Prozessoptimierung in Echtzeit
- Schnellere Produktentwicklungszyklen
"Der digitale Zwilling ist das Herzstück der Industrie 4.0. Er schlägt die Brücke zwischen physischer und digitaler Welt und ermöglicht völlig neue Fertigungskonzepte."
— Prof. Dr. Heinrich Schulz, Fraunhofer-Institut
KI und maschinelles Lernen in der Fertigung
Künstliche Intelligenz und maschinelles Lernen transformieren industrielle Prozesse in verschiedenen Bereichen:
Qualitätskontrolle
Computer Vision-Systeme können Fehler und Defekte mit einer Präzision erkennen, die das menschliche Auge übertrifft. Diese Systeme lernen kontinuierlich und verbessern ihre Erkennungsraten durch die Analyse von immer mehr Daten.
Predictive Maintenance
Durch die Analyse von Sensordaten können KI-Systeme potenzielle Ausfälle von Maschinen vorhersagen, bevor sie auftreten. Dies reduziert Ausfallzeiten und Wartungskosten erheblich.
Produktionsoptimierung
KI-Algorithmen analysieren komplexe Produktionsprozesse und identifizieren Optimierungspotenziale, die für Menschen oft nicht erkennbar sind. Sie können Produktionsparameter in Echtzeit anpassen, um die Effizienz zu maximieren und Ressourcen zu schonen.

KI-gestützte Visualisierung von Produktionsdaten in einer Smart Factory
Das Internet der Dinge (IoT) in der Fertigung
Das industrielle Internet der Dinge (IIoT) verbindet Maschinen, Werkstücke und Systeme zu einem intelligenten Netzwerk. Sensoren erfassen kontinuierlich Daten zu Betriebszuständen, Umgebungsbedingungen und Produktionsparametern.
Diese umfassende Datenerfassung schafft die Grundlage für:
- Transparenz über alle Produktionsprozesse
- Datenbasierte Entscheidungsfindung
- Automatisierte Reaktionen auf Prozessänderungen
- Umfassende Rückverfolgbarkeit von Produkten und Materialien
Auswirkungen auf die Arbeitswelt
Die zunehmende Automatisierung wirft Fragen hinsichtlich der Zukunft der Arbeit auf. Während einige repetitive und gefährliche Tätigkeiten von Robotern übernommen werden, entstehen gleichzeitig neue Berufsbilder und Anforderungen.
Veränderung des Kompetenzprofils
Mitarbeiter in der Industrie 4.0 benötigen neue Fähigkeiten:
- Technisches Verständnis für komplexe Systeme
- Datenkompetenz und Analysefähigkeiten
- Problemlösungskompetenz
- Flexibilität und lebenslanges Lernen
Mensch-Roboter-Kollaboration
Die optimale Fabrik der Zukunft nutzt die komplementären Stärken von Mensch und Maschine. Während Roboter Präzision, Ausdauer und Kraft bieten, bringen Menschen Kreativität, Flexibilität und Urteilsvermögen ein.
Nachhaltigkeit durch intelligente Automation
Ein oft übersehener Aspekt der Industrie 4.0 ist ihr Potenzial für mehr Nachhaltigkeit in der Fertigung. Intelligente Automatisierungssysteme können:
- Den Energieverbrauch durch optimierte Prozesse reduzieren
- Materialverbrauch und Ausschuss minimieren
- Ressourceneffizienz durch präzise Steuerung verbessern
- Die Lebensdauer von Maschinen durch vorausschauende Wartung verlängern
Fazit: Die Zukunft der industriellen Fertigung
Die industrielle Automation 4.0 repräsentiert einen fundamentalen Wandel in der Fertigungsindustrie. Die Integration von Robotik, KI, IIoT und Datenanalyse schafft intelligente, vernetzte Fabriken, die flexibler, effizienter und nachhaltiger produzieren können.
Unternehmen, die diese Technologien erfolgreich implementieren, werden in der Lage sein, schneller auf Marktanforderungen zu reagieren, Kosten zu senken und qualitativ hochwertigere Produkte herzustellen. Die größte Herausforderung liegt darin, die technologische Transformation mit der Entwicklung der Belegschaft in Einklang zu bringen.
Die Fabrik der Zukunft ist nicht nur automatisiert, sondern auch intelligent, vernetzt und menschenzentriert. Sie vereint das Beste aus beiden Welten: die Präzision und Effizienz der Robotik mit der Kreativität und Anpassungsfähigkeit des Menschen.
Kommentare (4)
Martin Klein
24. Juni 2024Als Produktionsleiter in einem mittelständischen Unternehmen finde ich die Möglichkeiten von Industrie 4.0 faszinierend. Wir haben vor kurzem kollaborative Roboter in unsere Montagelinien integriert und konnten dadurch die Effizienz deutlich steigern. Der Artikel gibt einen guten Überblick über die verschiedenen Technologien.
Claudia Meier
26. Juni 2024Der Artikel spricht wichtige Punkte an, aber ich vermisse eine kritischere Auseinandersetzung mit den sozialen Folgen der Automatisierung. Was passiert mit den Arbeitnehmern, deren Jobs durch Roboter ersetzt werden? Nicht jeder kann umgeschult werden, und wir müssen über gesellschaftliche Lösungen nachdenken.
Kommentar hinzufügen